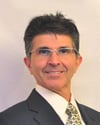
By Joe Giacona, Market Manager - Transportation
Sometimes we come across a bit of information that leads to a discovery about something we have long taken for granted. This new learning allows us a better understanding of how things function in a world that’s increasingly driven by technology.
A routine supermarket visit to purchase fruits, vegetables, meats and dairy items can yield one of those “ah hah” moments, especially when you look deeper. Take fruits and vegetables. There is such a wide selection - especially those that are on the shelf in the off-season! Where did they come from? California, Peru, New Zealand? How did they arrive at the peak of freshness? These are intriguing questions that offer “food” for thought.
In my years of experience within the transport refrigeration market, I appreciate the know-how, the people, products and technology that allows the movement of fresh food over long distances through what we call the food chain. This chain begins at the source, the point at where the food is picked and ends at your local grocery store. No matter what the cargo, the ‘chain’ of temperature control must remain unbroken over hundreds or thousands of miles to assure quality, maximize freshness and deliver value.
For the most part, refrigerated cargo is transported in either an ocean-going container or an over-the-road trailer/truck body with an integrated refrigeration or “Reefer” unit. These state-of-the-art machines are capable of maintaining precise temperature control throughout their interiors. They’re super-efficient because they balance temperature, air flow, and reliability.
On the surface, you’d think that temperature control is the most important – and you would be right. Almost. With sophisticated microprocessor controls, reefer units are designed to control cargo temperatures to within +/- ½ degree of set-point for extended periods of time over a wide variety of ambient conditions. However, temperature control cannot happen without precise air flow that moves air efficiently and effectively in every nook and cranny of the trailer to preserve those delicate fruits and leafy veggies we love. To protect the supermarket’s investment in its precious produce, the whole system must perform reliably over years of service.
Since the whole process is powered by some form of renewable energy or fossil fuel, it also must operate at maximum efficiency.
Our fans provide the critical ventilation that boosts the food-preserving performance of commercial transport units’ temperature controls. Designed to survive climate extremes and road shock, they allow precise delivery of air reliably and efficiently. Our food transport customers depend upon ebm-papst fans’ ability to meet their containers’ and trucks aerodynamic, electrical, and operational requirements day after day, month after month, year after year without fail.
The next time you purchase those delicious Chilean grapes or Mexican mangos in January, remember the combination of transport components and controls it took to deliver them across the food chain and unblemished to your table. Now that’s food for thought!
Read part 2 of this blog series: What's that fan doing in my food chain? Part 2
About Joe Giacona
Joe Giacona knows that HVACR components within transportation systems must deliver performance and reliability over the long haul. As market manager – transportation at ebm-papst, Joe’s 30+ years of diverse experience in HVACR help him recommend the best ebm-papst products to heat and cool customers’ buses, trains, trucks and other vehicles across North America. Joe actively supports the company’s market development, forecasting, field sales coordination and customer relations. He holds a B.S. in physics from Brockport State College and a B.S. in industrial engineering from the University of Buffalo. In his free time, Joe enjoys cooking for his family, do-it-yourself projects, keeping his 1960 Corvette Roadster in peak form, and making wine from New York and California grapes.