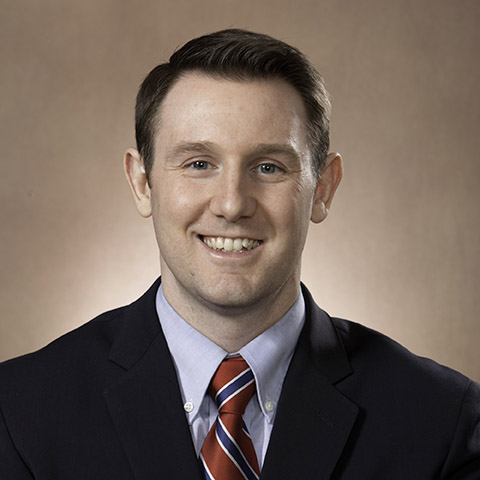
by David Hillburn, Business Development Manager - Heating
Recently I joined ebm-papst as a Business Development Manager to support the North American heating market. My previous experience includes design of combustion systems for industrial furnaces and kilns; so when I joined the company I had a good foundation in the application of various combustion systems and components but not in the manufacturing of these components. In March I toured two of our German manufacturing facilities in Landshut and Mulfingen in order to gain a more intimate knowledge of our products and how they are manufactured. Besides a new found love for pretzels, wheat beer, and white sausage, courtesy of the Hofbrauhaus, here are some lasting impressions of the facilities and trip.
Landshut, Germany and Mulfingen, Germany
Landshut and Mulfingen an overview
Landshut, situated approximately 45 miles northeast of Munich on the Isar River, produces the majority of our gas blower products. This includes the RG, NRG, G1G and G3G series blowers along with the recently acquired GB055 and GB057 gas valve lines. Mulfingen, our world headquarters and largest facility, produces the large G3G250-MW premix gas blower, M3G series motors and electronics along with a plethora of other products including our axial fan line and centrifugal blower/impeller products.
A large vertically integrated company
My previous employers were small companies, so I now find myself giving presentations that show stats such as 10,564 employees worldwide at 18 production sites and 58 sales offices. While touring the factories it felt like I met all 10,564 of these employees and they were working busily in various functions. Be it die-casting motor brackets, winding motor bobbins, stamping motor stators, checking printed circuit boards or assembling complete blowers. The factories were are state of the art manufacturing facilities, very vertically integrated and very automated. I saw these automation capabilities firsthand with the NRG118 assembly line in Landshut which produces an impressive number of gas blowers daily.
Reinvestment and R&D
Another key to success is our reinvestment into our facilities. On the A tour of our Landshut factory I viewed an impressive collection of climate chambers, halt testing machines and a new gas laboratory. At our facilities in Mulfingen I saw one of the largest combination air flow and sound chambers I’ve ever seen (big enough to park a truck in). I also toured rooms with racks and racks of fans running life cycle tests. So when we talk about quality and reliability it’s clear that is derived from continuous testing and commitment to reinvesting.
A company is only as good as its people
While the settings may be different, Landshut a small European city with a slightly metropolitan feel and Mulfingen a quaint rural village, the corporate mentality and image bridged the gap. At both facilities the people I met were not only knowledgeable and polite but happy to talk and discuss what they were doing within the organization. When asked to explain a process or a facet of design, they not only took the time to explain it but would walk me through the process, show me every piece that went into it and then bring me to a board similar to the one below so I could study the part or assembly further.
GB055 E01 Gas Valve Components
This level of cooperation and professionalism was displayed by all employees I talked to and it helped to make a business trip abroad a very productive and memorable experience. I look forward to future factory visits and traveling with my German colleagues to our heating customers in North America.