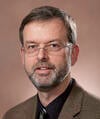
Armin Hauer, Advanced Technology Manager
An article in a recent issue of Sustainable Business examines the potential impact of the uncertain supply of rare earth magnets on manufacturing EC motors, noting that EC technology is reliant on rare earth elements. But this isn’t always the case…
The manufacturers of electric motors struggle to predict the future costs of rare earth elements. As a result, user circles often regard permanently excited electric motors, which are particularly energy-efficient, as expensive. But highly efficient electric drives don’t necessarily depend on strong rare earth magnets. For example, "simple", cost-effective and – above all – readily available ferrite magnets suffice for energy-saving EC fan motors with an external rotor design. In some cases, these reach motor efficiencies of more than 90 percent.
How an EC motor works
A brushless DC drive (BLDC motor), a BLPM motor or an electronically commutated (EC) motor – exactly which motors are in the rare earth element discussion? These are all actually different names for permanently excited synchronous motors. These motors use electronic drives that are either AC line-powered or that use DC power supplies. The BLDC/BLPM motors usually operate with square-wave currents (block commutation). In contrast, EC motors can operate with both square-wave currents and with sinusoidal currents (sinusoidal commutation). The latter method achieves a significant noise and vibration reduction over the block commutation method. The design with sinusoidal currents corresponds to the classic synchronous motor.
Exploded view: The permanently excited synchronous motor, also called brushless direct current motor or EC motor.
An EC motor always requires a drive electronic that includes an inverter for the control of sequential and reversing current flows in all cores of the armature. This electronic commutation determines the strength and rotational speed of the resulting magnetic field that the armature generates. The permanent magnet rotor responds by revolving synchronously with the rotary field of the armature. In contrast, the speed of AC line-powered asynchronous motors depends on the frequency of the supply voltage and on the motor load. The torque-speed characteristic of an EC motor mimics a DC shunt motor, because both motor voltage and shaft speed, as well as motor current and shaft torque, correlate linearly. The angular rotor position is continuously determined by either sensor hardware in the motor, or the inverter senses the so-called counter-electromotive force and the motor currents for resolving the position mathematically. The idle motor speed depends on the applied voltage and the number of turns of the armature windings. Within the physical parameters of output power, torque and temperature exposure, nearly arbitrary motor speeds can be reached slip-free and synchronously with the rotating magnetic field. These speeds are completely independent of the AC line frequency.
Dynamic requirements determine magnet choice
As a result of their unique motor characteristics, external rotor EC fans seldom need strong rare earth elements. That type of magnetic quality is really only needed to minimize the moment of inertia for very dynamic servo motors.
Why our EC motors don’t need rare earth magnets
ebm-papst GreenTech EC motors for energy-efficient fans remain undisturbed by rare earth element scarcity, because the armature of a GreenTech EC motor is located inside and is surrounded by the rotor.
Cutaway: Centrifugal fan with external rotor motor.
Our energy-efficient fans remain undisturbed by rare earth element scarcity because the arrangement with external rotor motor achieves a higher torque than an internal rotor motor of the same size, magnet system and magnet thickness. An internal rotor motor has a restricted magnet volume, a reduced air gap surface and smaller radius. External rotor motors that use hard ferrite magnets cleverly applied to fans and blowers attain torque and efficiency levels that internal rotor motors can achieve only with rare earth magnets, due to limited volume and size.
A fan motor design with an external rotor has an additional advantage: The fan impeller mounts directly to the outer rotor, directly to the motor "housing". The result is a compact axial length and superior self-cooling of the external rotor motor.
To further discuss how our EC motors are different, contact us.
Dr Jürgen Schöne, R&D Director of Aerodynamics and Motor Technology at ebm-papst Mulfingen,Werner Müller, Manager of Motor Development at ebm-papst Mulfingen, Armin Hauer, Advanced Technology Manager at ebm-papst Inc.