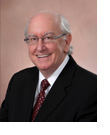
by Bob Sobolewski - President & CEO
If one thing was evident at last month's Air Conditioning, Heating and Refrigeration (AHR) Expo in New York, it's that innovation and sustainability must go hand in hand.
AHR provides us with an opportunity to meet our partners, suppliers and customers face to face. Every year, the show renews our belief that energy savings and resource conservation are a priority. It renews our commitment to our GreenTech philosophy: that every product we develop must exceed its predecessor in terms of efficiency and economy. At this year’s expo, we gave a group of editors and industry experts a re-cap of our company’s achievements in 2013.
2013 Growth
2013 marked the 50th anniversary for the ebm-papst Group. Founded by Gerhard Sturm and Heinz Ziehl in 1963 with only 35 employees, the company now has 11,400 employees at 57 sales offices and 18 production facilities worldwide. ebm-papst Group grew 10 percent to around 730 million euros ($993 million) for the first half of the current fiscal year (April 1 - September 30, 2013). Over the past three years, the global company has grown by 37 percent.
The double-digit growth of ebm-papst USA last year was fueled by a growing need for climate control across nine major markets and the applications within each, as well as employees’ focus on exceeding customer needs.
Awards for AxiTop
The epylen wood-plastic composite AxiTop diffuser, introduced in 2012 as a new, passive component in ebm-papst 800 and 910 mm series fans, recently earned ebm-papst top honors at the MATERIALICA trade fair in Munich. AxiTop was honored in the Material category for its combined energy savings, noise reduction and energy efficiency.
US production of Axial and RadiPac fan assemblies
Over the past decade, we’ve expanded our product portfolio into much larger dimensions. Ten years ago, a large ebm-papst fan was 500mm to 630mm in diameter. Now, we’re selling fans up to 1.5 meters in diameter that are used in large-scale refrigeration and ventilation applications.
To increase responsiveness to our NAR customer base, we began localizing production of our larger axial fans, which are typically used in condensers and chillers, and for our RadiPac backward curved impellers used in rooftop A/C units, computer room A/C units and other applications.
Localizing production of these fan models also helps us customize the venturi, housing, mounting and paint color specs to customers’ requirements, speed turnaround and further reduce our transport-related carbon footprint.
GreenTech in practice at our Farmington, CT production facility and offices
Last year, our production facility completed installation of a new large capacity powder paint application system complete with an automatic feed system and new spray guns. The guns allow for more even coating and better use of powder at lower air pressures – further reducing powder spray waste and improving paint quality. The new powder paint system’s dual cyclone technology feeds back (recycles) the 40% of powder that hits the parts and falls into the bottom of the paint booth – increasing our actual powder usage efficiency to about 95%. As a result, production has increased our powder spray efficiency, disposed of less scrap powder, achieved higher quality for painted parts, and significantly reduced color change times.
We also replaced all highbay lights in our production facility and warehouse, and all outdoor lighting around the plant with new energy efficient LED fixtures. Energy savings for this recent installation will be measured throughout 2014.
A comprehensive new high-efficiency 15-unit HVAC system with an average Seasonal Energy Efficiency Ratio (SEER) rating of 12.0 is being installed to replace a circa-1999, 9.0 SEER-rated 200 ton cooling system on the roof of our US headquarters. Based on today’s energy rates, we expect that these new HVAC units will save the company 20% per year in electricity expense. To further boost efficiency, a sophisticated web-based control system will allow for in-house and remote monitoring. What’s more, the new HVAC units employ ebm-papst impellers!