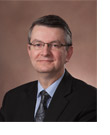
By Don Beckwith, Senior Vice President – Finance and Administration
Great things happen when employees know their work is valued, when they’re encouraged to take on new challenges and when they have opportunities to contribute to a greater good.
Tom Rath and Jim Harter, Ph.D., authors of Wellbeing: The Five Essential Elements, reveal that wellbeing encompasses five distinct, interrelated elements – Career, Social, Financial, Physical, and Community. All of them affect the bottom line.
Some of the world’s most successful corporations have put non-traditional but innovative practices in place to keep their employees happy, healthy and productive.
At ebm-papst, helping employees improve the quality of their lives has and will always be a part of the ebm-papst DNA. Here are four ways we support our employees.
-
Open Communication
Effective communication builds trust. Our open-door policy allows employees to express their ideas and concerns. When managers openly communicate with their teams and when employees understand the value of their roles, our entire organization becomes more productive and innovative.
-
Social Events
Community — along with a dedication to environmental sustainability — is a big part of the ebm-papst culture. As we add employees, e-mails and conference calls become more convenient than face-to-face interactions. Yet without outlets for personal interaction, employees may feel removed from the corporate identity. ebm-papst regularly celebrates employee-centered events such as our Every Day is a GreenDay picnic where local fresh foods are sourced, Apple Day where apples are brought in from a local farm and shared, ice cream afternoon breaks and more. These events foster camaraderie and create a positive atmosphere in the workplace.
-
Explaining the Big Picture
Because employees need to understand how their accomplishments contribute to the overall success of the company, it’s important that we regularly share our overall goals. At least twice per year, we hold a companywide meeting to address the current state of business, future plans and projections. This further reinforces a sense of community and encourages teamwork.
-
Promote Wellness
Employee wellness is important for any business trying to reduce health care costs, but it isn’t the only benefit. Wellness improves employee morale, increases employee retention and creates more productive workers. A wellness program encourages healthy habits to prevent serious health conditions later. Yearly, we hold a wellness fair that incorporates healthy eating tips, blood pressure and cholesterol screenings and information on the prevention and diagnosis of serious health conditions. We also offer flu shots and gym membership reimbursement programs.
When our employees’ lives are happy, healthy and balanced, the entire organization benefits. The proof? We experience it every day in the innovative products we create, the efficient ways we produce them and the responsive customer service we provide.